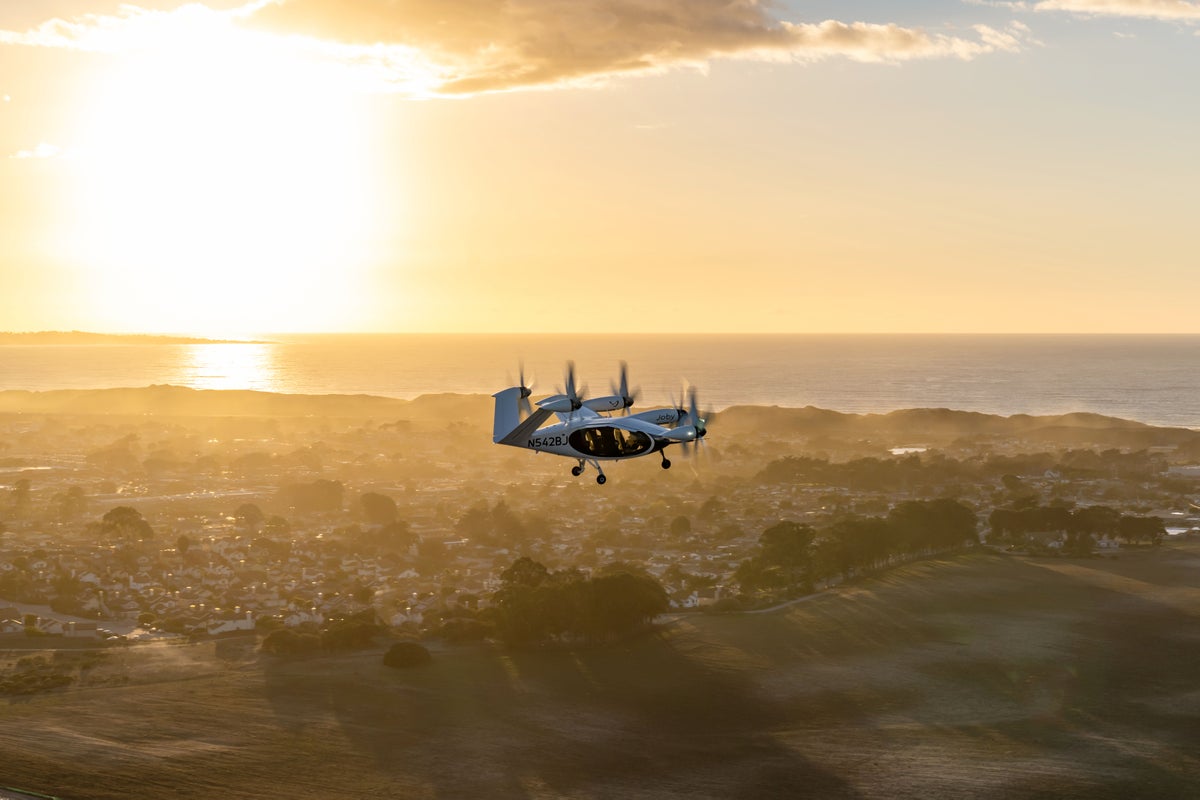
When the electric air taxi revolution arrives, you probably won’t it hear coming. A remarkable feature of an electric vertical takeoff and landing (eVTOL) aircraft is how quietly it flies, scarcely noticeable amid typical city traffic sounds. Unlike a helicopter, there’s no pounding, 90-decibel “thwop, thwop, thwop.” In contrast, eVTOL aircraft use multiple small propellers that spin half as fast as a chopper’s rotor—avoiding the annoying, low-frequency sound pulses created by the big whirling blades.
Electric motors, which are quieter than helicopters’ turbine engines, also help keep any racket to a minimum. “The latest air taxi designs, such as those from leading builders like Joby and Archer, deliver a 20- to 25-decibel reduction in noise levels compared to helicopters,” says Mark Moore, the trailblazing engineer who led the development of NASA’s X-57 Maxwell electric airplane. That means that eVTOLs could be four or five times less noisy to nearby listeners. Beyond offering quieter flights, these new machines should also be significantly safer, greener and cheaper to fly than helicopters. Moore maintains that electric air taxis are uniquely suited for what the aviation industry calls urban air mobility (UAM) services, enabling normally gridlocked travelers to “take advantage of the third dimension to escape the ant trails on the ground.”
More than two dozen major eVTOL builders have been founded in the past decade, and a few are nearing commercial certification from the U.S. Federal Aviation Administration or its European counterpart, the European Union Aviation Safety Agency (EASA). Each company is working on its own homegrown aircraft design, but all have the same goal: to provide on-demand air trips no longer than 18 to 25 miles—the “sweet spot” range for first-generation, battery-electric eVTOL taxis. These short, high-speed hops could carry commuters between city centers and airports or transport cargo and packages. Militaries may want eVTOLs for casualty evacuations or logistical supply. Other potential uses include air ambulances, donor organ delivery and police transport, as well as scheduled shuttles and ecotourism trips—and, of course, personal flying cars.
On supporting science journalism
If you're enjoying this article, consider supporting our award-winning journalism by subscribing. By purchasing a subscription you are helping to ensure the future of impactful stories about the discoveries and ideas shaping our world today.
Distributed Electric Propulsion
In 2016 Moore, who co-founded Uber Elevate, an air taxi offshoot of the ride-sharing company, and his colleagues outlined the emerging industry’s basic business model in a seminal white paper entitled “Fast-Forwarding to a Future of On-Demand Urban Air Transportation.” It galvanized the nascent UAM industry by declaring that the necessary technology had finally arrived. “What had previously been science fiction” was suddenly becoming a going enterprise, Moore recalls. Uber Elevate soon assembled potential players including budding airframe builders, airline companies, auto makers and transport service providers, as well as potential financiers and operators of new vertiports—airports for vertical-lift aircraft.
Huge funding deals involving Silicon Valley billionaires and big corporations followed, with more than $1 billion raised in the first quarter of 2020 alone. But after a turbulent period of hype and overexpansion, Uber’s air taxi venture nosedived that same year, forcing the company to sell its Elevate division to Santa Cruz, Calif.–based electric aircraft company Joby Aviation. By then, however, the electric air taxi industry had established a coherent business plan based on a workable technology: distributed electric propulsion.
In distributed electric propulsion, multiple small electric propulsors (individual propellers, each with its own electric drive motor) are placed along the wings, tail or airframe, where they work in concert to generate thrust, lift and control forces. “What’s key is that they enable novel rotorcraft designs to meet noise and emissions regulations in urban areas,” says aviation pioneer John Langford, former CEO of Virginia-based Aurora Flight Sciences. The company, now Boeing-owned, built several early electric aircraft and eVTOLs, mostly for the Pentagon.
Noise reduction isn’t the only perk of this propulsion approach. Many propellers offer safety redundancy that helicopters, with only one or two rotors, cannot, Moore says. If one propulsor fails, others can take the load. And unlike helicopter turbine engines that spew fossil fuel exhaust, he notes, “electric motors are low- or zero-emissions.”
The engineers and designers creating these craft couldn’t, however, simply swap turbines for electric motors. “Replacement with electric power would mean less performance in many cases,” Langford points out. “The low energy density of batteries means that electric aircraft are best suited to short-range missions—less than 200 miles, often way shorter than that.” But he adds that eVTOLs’ high efficiency and low maintenance needs can mean lower operating costs—the big draw for electric air taxi proponents.
Key among all the designs, therefore, is minimizing weight to avoid overtaxing the batteries—the weakest link among eVTOL systems—especially during takeoffs and while hovering. Many current eVTOL aircraft are being optimized to replace 60- to 90-minute car commutes with 10- to 20-minute air taxi rides flying at perhaps 150 mph. That’s why nearly all air taxi designs feature lightweight carbon-composite airframes.
Air taxi Taxonomy
With hundreds of varied air taxi vehicles in the works globally, it’s useful to categorize them by their general designs. Someone well equipped to provide such a taxonomy of air taxis is Tom Muniz, chief technology officer of San Jose, Calif.–based Archer Aviation. He is a veteran of multiple eVTOL ventures, including Zee.Aero, Kittyhawk and Wisk Aero (the latter of which is now owned by Boeing).
“The simplest category is the multicopter eVTOL,” Muniz says. “They resemble a standard drone in that they have multiple lift propellers but no wings, which limits range and speed.” Without wings’ ability to generate high aerodynamic lift forces quietly, multicopters tend to be noisier than other types, he notes.
Germany’s Volocopter and China’s EHang are two companies that produce small, multicopter-type eVTOLs. At the upcoming Summer Olympics in Paris, Volocopter hopes to fly passengers between five recently completed municipal vertiports in its two-seat VoloCity demonstrator. Meanwhile the Civil Aviation Administration of China recently cleared EHang to mass-produce its pilotless EH216-S eVTOL, which can operate autonomously while carrying two passengers.
Next in terms of technical complexity, Muniz explains, are the “lift-and-cruise” designs. These aircraft merge the multicopter layout with the conventional fixed-wing airframe configuration, enabling longer ranges and higher speeds. Generally, an array of skyward-facing propellers positioned around the aircraft create vertical lift during takeoffs. One or more fixed pusher props in the rear then send the craft forward, transitioning to energy-efficient wing lift, Muniz says. When it’s time to land, the lift propellers take over again.
The CityAirbus NextGen eVTOL prototype, from Airbus UAM, a Germany-based division of the European multinational aerospace company, is a new lift-and-cruise air taxi that is expected to take to the air in late 2024. It seats a pilot and three passengers and features a maximum range of 50 miles and a cruise speed of 75 miles per hour. Another lift-and-cruise eVTOL is the recently certified 4,400-pound, five-seat Prosperity from Shanghai-based AutoFlight. Earlier in the year, a test craft completed a 20-minute intercity flight between the Chinese cities of Shenzhen and Zhuhai—a trip that takes three hours by car.
One notable contender among the new air taxi designs is not an eVTOL at all but an eSTOL—an electric (or extreme) short takeoff and landing aircraft, under development by Langford’s current venture, Electra.aero, based in Manassas, Va. Electra’s two-seat, hybrid-electric eSTOL demonstrator, the EL-2 Goldfinch, resembles a nimble, slow-flying crop-duster plane. But the Goldfinch recently showed that it can safely operate from an airstrip less than 170 feet long—much shorter than what a standard fixed-wing plane requires. (For comparison, a fully loaded Cessna 172, a common small aircraft, generally needs about 960 feet of runway.)
“Goldfinch has eight electric propellers along the wing’s leading edge that significantly boost lift by blowing air over the wing, increasing the effective air speed and hence the aerodynamic lift they generate,” Langford explains, adding that this extra lift “helps enable ultrashort, low-speed landings.” Together with large wing flaps that extend like an airliner’s, along with an oversized horizontal tail stabilizer for control, Electra’s “blown-lift” eSTOL prototype is paving the way for a nine-passenger commercial version. This larger aircraft, Langford says, should be able to operate from 295-foot-long fields—a layout that could fit at some of Manhattan’s current riverside heliports.
Joby and Archer
A more complex variation of the lift-and-cruise eVTOL is the “vectored thrust” type, in which articulated propulsors tilt to provide vertical or horizontal thrust as needed, Archer’s Muniz says. He points to his company’s Midnight vehicle and Joby Aviation’s S4 2.1 eVTOL as the principal examples.
Archer’s Midnight, a 6,500-pound craft with room for a pilot and four passengers, has a dozen forward-facing electric propellers on the wings and tail. Six tilt propellers provide lift for vertical takeoff and landing, as well as thrust for forward movement; six fixed lift propellers operate only during vertical flight. The company says this craft can reach speeds up to 150 mph. Joby’s eVTOL, called S4 2.1, is a 4,800-pound vehicle with a pilot and three passengers that’s driven by six tilting propulsors. It has a maximum speed of 200 mph.
Both companies have joined the U.S. Air Force AFWERX Agility Prime program, which is spending hundreds of millions of dollars to acquire air taxis for testing and evaluation by NASA engineers. Last September Joby delivered its first production prototype eVTOL aircraft to Edwards Air Force Base, says Didier Papadopoulos, the company’s president of aircraft OEM (original equipment manufacturer).
Air taxis need to operate at a cost of around $3 per passenger mile to make a profit, according to Joby’s business model, which is based on Uber’s huge ride-hailing database. Joby plans to operate all day with only six- to eight-minute stopovers to transfer passengers and recharge batteries, Papadopoulos says. Considering the tight costsand specialized needs, he adds, company engineers are developing all the components of their aircraft in-house. That vertically integrated supply chain contrasts with Archer’s lower-cost approach, which uses many off-the-shelf components, according to Muniz, barring motors, batteries and control computers. And whereas Archer has chosen to use Tesla-proved “automotive-style” cylindrical lithium-ion batteries, Joby has reportedly opted for a lithium-nickel-cobalt-manganese-oxide battery pack using more compact, lighter-weight pouch cells.
Moore views the two differently sourced machines as “a Ferrari versus a Toyota Camry.” Whether either vehicle, or any of their many competitors, can find widespread customer acceptance among the traveling public remains to be seen.
"electric" - Google News
June 14, 2024 at 07:07PM
https://ift.tt/759IugJ
Electric Aircraft Are Quietly Sneaking Up on Us - Scientific American
"electric" - Google News
https://ift.tt/icg6V3W
https://ift.tt/dzuFEOL
No comments:
Post a Comment