There’s a revolution brewing in batteries for electric cars. Japanese car maker Toyota said last year that it aims to release a car in 2027–28 that could travel 1,000 kilometres and recharge in just 10 minutes, using a battery type that swaps liquid components for solids. Chinese manufacturers have announced budget cars for 2024 featuring batteries based not on the lithium that powers today’s best electric vehicles (EVs), but on cheap sodium — one of the most abundant elements in Earth’s crust. And a US laboratory has surprised the world with a dream cell that runs in part on air1 and could pack enough energy to power aeroplanes.
These and other announcements rely on alternative designs to the conventional lithium-ion batteries that have dominated EVs for decades. Although lithium-ion is hard to beat, researchers think that a range of options will soon fill different niches of the market: some very cheap, others providing much more power. “We’re going to see the market diversify,” says Gerbrand Ceder, a materials scientist at the University of California, Berkeley.
The pursuit of better car batteries is fierce, in large part because the market is skyrocketing. More than a dozen nations have declared that all new cars must be electric by 2035 or earlier. The International Energy Agency forecasts that the global stock of EVs on the road will rise from 16.5 million in 2021 to nearly 350 million by 2030 (see go.nature.com/42mpkqy), and that demand for energy from EV batteries will reach 14 terawatt hours (TWh) by 2050, which is 90 times more than in 20202.
Car batteries have a stiff list of requirements. They need to pack a lot of energy into as little material and weight as possible so that cars can go farther on a single charge. They need to provide enough power for acceleration, recharge fast, have a long lifespan (the common standard is to withstand 1,000 full recharging cycles, which should last a consumer 10–20 years), work well across wide temperature ranges and be safe and affordable. “It’s very hard to optimize all these things at once,” says Linda Nazar, a battery researcher at the University of Waterloo, Canada.
So researchers are pursuing a plethora of options, with different targets in mind. The US Department of Energy’s (DoE’s) Battery500 programme, launched in 2017, is aiming for a cell energy density of 500 watt-hours per kilogram (Wh kg–1), a 65% boost compared with today’s best products. The PROPEL-1K programme, launched last year by the US Advanced Research Projects Agency–Energy, is ambitiously aiming for a longer-term goal of 1,000 Wh kg–1. As for cost, the DoE’s Vehicle Technologies Office is aiming to hit US$60 per kilowatt hour by 2030, about half today’s prices, which it reckons will mean that the price of electric cars will break even with the cost of those powered by gas guzzling petrol engines (see ‘Powering up’).
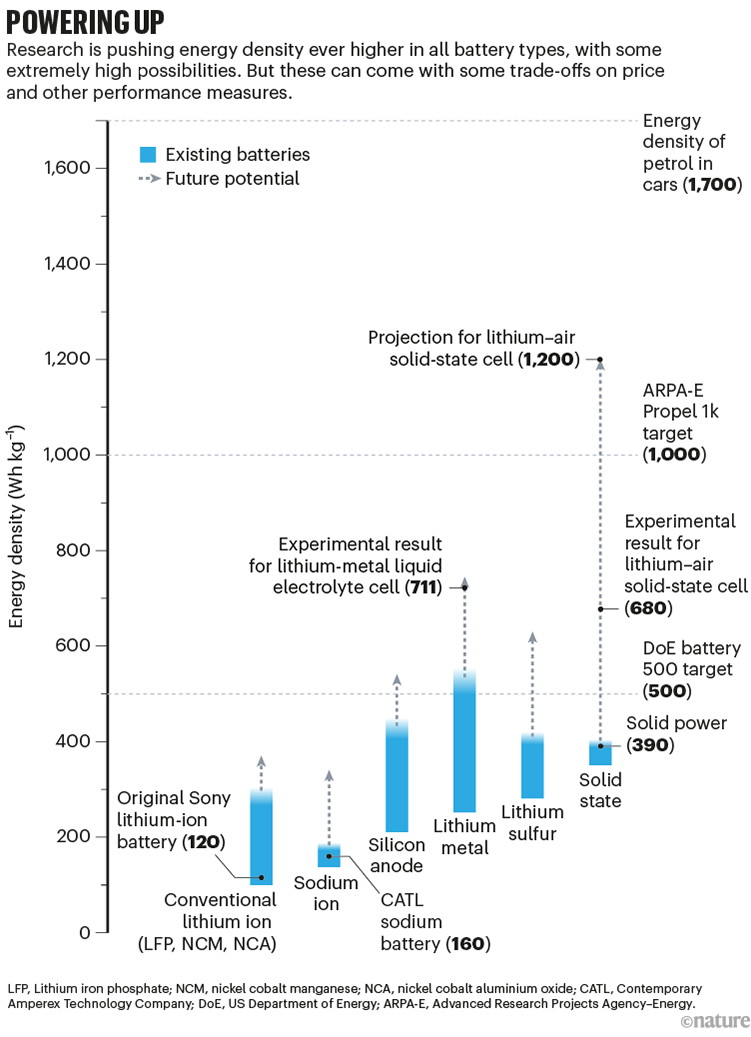
It’s hard to pin down where things stand. Commercial announcements about yet-to-be-released batteries or cars sometimes emphasize one metric over others, and proprietary claims can be impossible to check until batteries have been tested for years in real-world cars. But it’s clear that decades of work on variants such as solid-state and sodium batteries are finally coming to fruition, says Nazar. As for the far future, plenty of battery chemistries remain tantalizing possibilities. “Now everyone has accepted battery development is really important, everyone is tripping over themselves to do it,” she says.
Electrode evolution
Batteries are effectively chemical sandwiches, which work by shuttling charged ions from one side (the anode) to the other (the cathode) through some intermediate material (the electrolyte) while electrons flow in an outside circuit. Recharging the battery means shunting the ions back to the anode (see ‘How a battery works’).
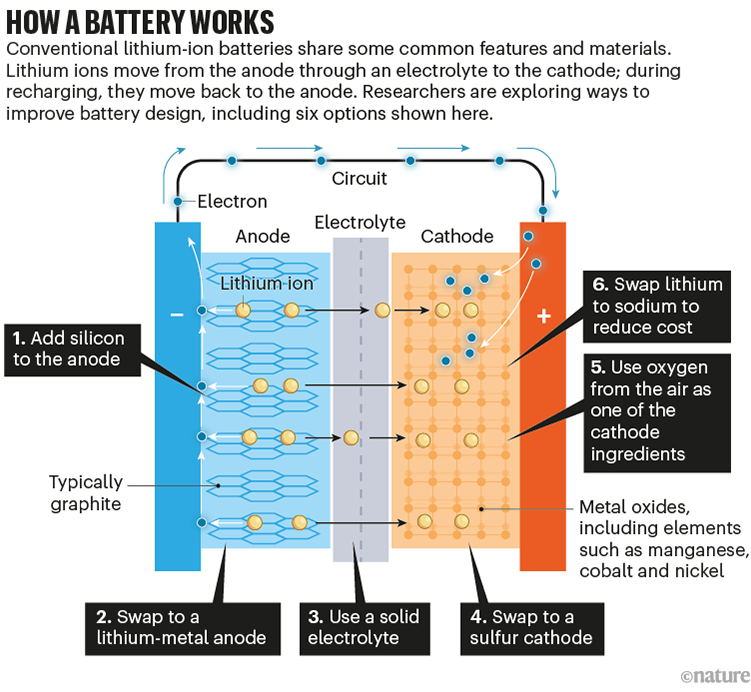
Today, most electric cars run on some variant of a lithium-ion battery. Lithium is the third-lightest element in the periodic table and has a reactive outer electron, making its ions great energy carriers. The lithium ions travel between an anode usually made from graphite and a cathode made from a metal oxide, both of which host lithium ions between atomic layers. The electrolyte is typically an organic liquid.
Lithium-ion batteries have improved a lot since the first commercial product in 1991: cell energy densities have nearly tripled, while prices have dropped by an order of magnitude3. “Lithium-ion is a formidable competitor,” says Ceder. And with further scope for improvement, some say lithium-ion will be king for a long time. “I think lithium ion will for decades be the technology which powers electric cars, because it’s good enough,” says Winfried Wilcke, a recently retired scientist in Los Altos, California, who headed an IBM Research battery project from 2009 to 2015.
Most of the improvement in lithium-ion thus far has come from changes to the material of the cathode, resulting in multiple commercial cell types. One, popular in laptops, uses lithium cobalt oxide, which produces relatively light but expensive batteries. Others, popular in many cars, use a mix of nickel and cobalt with aluminium or manganese as a stabilizer (NCA and NCM). Then there’s lithium iron phosphate (LFP), which does without expensive cobalt and nickel but so far has relatively poor energy densities (see ‘Lithium-ion battery types’). LFP’s price has made it attractive and plenty of researchers and companies are working to improve it; US EV manufacturer Tesla notably decided in 2021 to swap to LFP batteries in its mid-range cars.
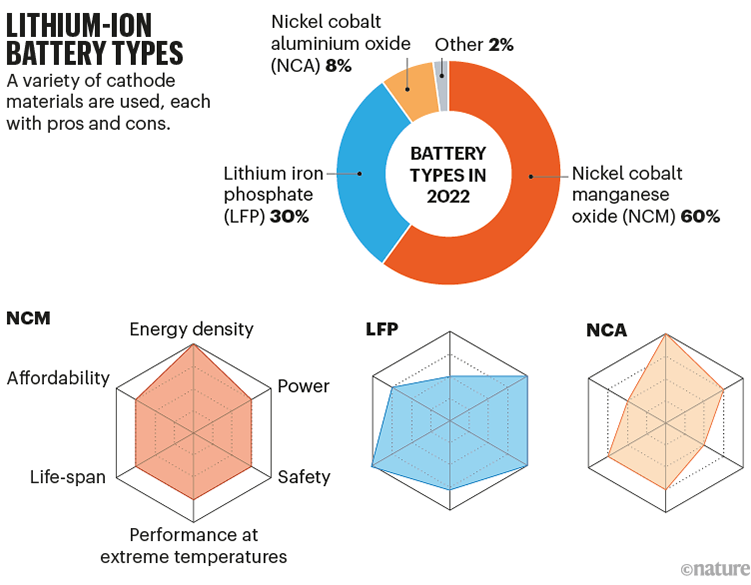
There is scope for more tweaks to the cathode. In NCM batteries, researchers have been paring back more-expensive cobalt in favour of nickel, which also provides a higher energy density. That path has led to commercial NCM811 battery cathodes with 80% nickel, and researchers are now working on NCM955, with 90% nickel.
Meanwhile, at the anode, one common option is to swap graphite for silicon, a material that can store ten times more lithium atoms per weight. The challenge is that silicon expands and contracts by around 300% during charge–discharge cycles, putting a lot of structural strain on the battery and limiting its lifetime.
Even better than a silicon anode is simply lithium itself. “You don’t have any wasted material,” says chemical engineer Brian Cunningham at the DoE’s Vehicle Technologies Office in Arlington, Virginia. In addition to cutting down on weight, this can speed up charging, because there is no waiting for lithium ions to slot in between any layers (this change, technically, makes the design a lithium-metal rather than a lithium-ion battery). But a big problem with this strategy is that during recharging, lithium tends to redeposit on the anode unevenly, with hotspots that form tendrils called dendrites, which can reach out through the electrolyte and short-circuit the battery.
Lithium-based batteries with better electrodes can, in theory, achieve huge energy densities, but often have trade-offs in terms of cell lifetimes or safety. Last year, one group of researchers in China reported a cell with a lithium-metal anode (and a type of lithium-rich cathode) that hit higher than 700 Wh kg–1 in the lab4. The group’s start-up firm, WeLion New Energy in Beijing, is aiming to develop and commercialize this battery, along with other options. Another aspirational idea offering high energy densities is a lithium sulfur (LiS) battery, with a lithium-metal anode and a sulfur cathode. But sulfur reacts with lithium to make soluble products that can deposit on the anode and kill the battery. LiS “has been tried for 30 years and it still has major challenges”, says Ceder.
With such troubles plaguing batteries with better electrodes, many say the most enticing solution is to replace the liquid electrolyte with a solid.
Solid idea
The idea of solid-state batteries is to use a ceramic or solid polymer as the electrolyte, which hosts the passage of lithium ions but helps to stem dendrite formation. Not only does this make it easier to use an all-lithium anode — with the attendant energy-density advantage — but getting rid of the flammable organic liquid also means removing a hazard that can cause fires. The cell architecture of solid-state batteries is simpler than that of liquid-based cells, says Nazar. And the solid batteries, in theory, work better both at low temperatures (because there’s no liquid to get more viscous when it’s cold) and at high temperatures (because the interfaces with the electrodes don’t suffer so much when it’s hot).
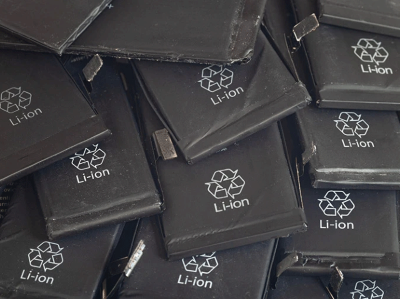
Could grinding up lithium batteries help to recycle them?
But there are challenges: in particular, how to manufacture a smooth, flawless interface between the layers. Also, the transport of ions through a solid tends to be slower than through a liquid, limiting power. And solid-state batteries require an entirely new manufacturing process. “From all we see, they will be more expensive,” says Ceder.
“Solid state has a big future. No question. But it’s bloody difficult to make it happen,” says Wilcke.
Some battery companies are moving forward with solid state. Colorado-based Solid Power in Louisville (partnered with car makers BMW and Ford), for example, has begun pilot-scale production of a solid-state cell with a silicon-based anode that they say hits 390 Wh kg–1, and California-based QuantumScape (which has signed deals with manufacturers including Volkswagen) has a solid-state battery that gets the advantages of a lithium anode with an even lower-weight, anode-less design. Lithium metal gathers at the anode side, but there is no need for a lithium plate there to start with. Some of these battery details are proprietary. QuantumScape has released some prototype performance data, but won’t say what its electrolyte is made from or what the energy density is of its intended first commercial product. In general, the touted higher energy densities for solid-state batteries are “unproven today at any sort of commercial scale”, says Ceder.
Actual cars powered by solid-state batteries seem to be perpetually on the horizon: Toyota’s original target date for commercializing them in the early 2020s has now slipped to the late 2020s, for example. When it comes to batteries, “Toyota has said a lot of things in the last ten years, none of which have come through,” cautions Ceder. But Nazar thinks the time frame in general is realistic. “I believe that in 2025, we’re probably going to see some market intrusion of some of these cells,” she says, especially given that there are some ambitious Chinese companies on the case. That includes the world’s largest battery manufacturer, Contemporary Amperex Technology (CATL), headquartered in Ningde.
Meanwhile, plenty of researchers are pursuing ways to improve solid state. Chemist Jennifer Rupp at the Technical University of Munich in Germany has founded a company, QKera, also in Munich, that manufactures ceramic electrolytes at half the usual 1,000 °C temperature. That both helps to limit carbon dioxide emissions from the furnaces used in the manufacturing process and helps to resolve some issues over binding the electrolyte to the cathode. Another promising angle, says Nazar, is a new class of oxyhalide electrolytes for solid-state batteries. Some of these are ‘gooey’ and so more flexible, which should ease manufacturing and make them less vulnerable to cracking5. And some have extremely high conductivity, letting lithium ions zoom through as if through a liquid rather than a solid, with associated power benefits6. Other firms are working on a solid-state version of LiS, says Cunningham.
The ‘pot of gold’ battery at the end of this solid-state rainbow, many say, would be a lithium–air design. This kind of battery uses a lithium-metal anode, and the cathode is based on lithium binding to oxygen that is pulled from the air and released again when the battery recharges. In part because a key cathode ingredient isn’t stored in the battery, this design can hold much more energy per kilogram. But the idea has long seemed speculative. “Some of my colleagues call it fairy-tale chemistry,” says Nazar.
Materials scientist Larry Curtiss at Argonne National Laboratory in Lemont, Illinois, and his colleagues hit the headlines in 2023 with a surprising paper showing a solid-state, experimental lithium–air battery tested over 1,000 cycles in the lab1. The team says its coin-sized test cell runs at about 685 Wh kg–1 and should be able to reach 1,200 Wh kg–1, four times what’s achievable with lithium-ion now and roughly comparable with the energy density of petrol in cars. The experimental system works using a new chemistry that surprised even the team studying it. Previous lithium–air battery projects, typically using liquid electrolytes, made lithium superoxide (LiO2) or lithium peroxide (Li2O2) at the cathode, which store one or two electrons per oxygen molecule. The new cell instead makes lithium oxide (Li2O), which can hold four. Those extra electrons translate to a higher energy density, and the system seems a lot more stable than previous efforts, which should lead to longer battery life.
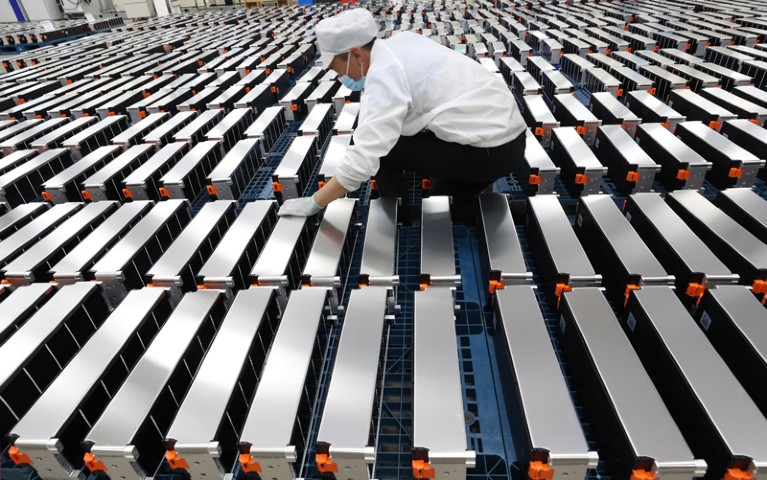
“It’s unbelievable what they did,” says Wilcke. “They can use ordinary dirty air with moisture and carbon dioxide and all the other crap that you find in unfiltered air. Not a problem,” says Wilcke. But many say they would like to see the effort replicated before getting too excited. And although it’s a great energy storage system, it’s unclear how it would work in practice — how you could get the air in and out, for example, and whether it can be built bigger and made to work with higher currents. “It’s definitely a much longer time horizon then than even lithium sulfur,” says Cunningham.
Curtiss says the team is thinking about aviation as the best application for the technology, given that it’s so energy dense. Wilcke agrees. Energy density is a “huge, huge factor in aircraft”, says Wilcke, who is bullish in particular on electric vertical take-off and landing craft, expected to be used as ‘flying taxis’. If that sounds like science fiction, an electric air taxi was licensed to fly in China — even without a pilot — in October 2023, and several companies make craft that can go a couple of hundred kilometres on lithium-ion batteries. Air taxis that can skip the traffic taking you from the airport to your hotel, Wilcke says, are an emergent industry that’s about to take off.
Price drop
As the quest continues for miracle batteries that pack in ever more energy, some scientists argue that the most pressing concern is the need to pick a battery chemistry that will be cheap and sustainable in the long run.
“The biggest challenges are resource-related,” says Ceder, who calculates that the projected 14 TWh needed for cars by 2050 will require 14 million tonnes of total metal. That’s a lot; for comparison, today’s global mining of lithium is about 130,000 tonnes per year, whereas cobalt is nearly 200,000 tonnes and nickel 3.3 million tonnes — that’s for all purposes, including non-EV batteries and, for nickel, stainless steel. The quantity needed makes it important to choose metals that are not scarce or expensive and do not cause excessive environmental damage when they are mined.
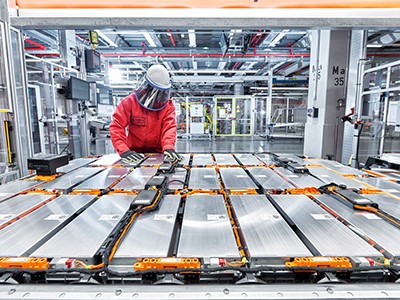
Electric cars and batteries: how will the world produce enough?
Plenty of researchers and companies are trying to make batteries that don’t use nickel, cobalt or other expensive metals. QuantumScape, for example, says its batteries have this advantage, as do lithium–air concepts, LiS (if it can be made to work), other experimental materials7 and the already commercial LFP cathodes (although LFP might put a strain on phosphorus resources if that technology scales up a lot). Ceder is looking at alternative cathodes called disordered rocksalts (DRX)8. These rely on the idea that lithium ions can just meander through a crystalline cathode rather than taking an ordered path through layers, and thus the cathode can be made with almost any transition metals. Ceder’s team favours manganese and titanium. He expects the first batteries with DRX cathodes to be cheaper than current lithium-ion cells and to achieve comparable energy densities.
Perhaps the ultimate goal is to get rid of the lithium itself — a metal that has seen wild price swings thanks to booming demand and supply pinchpoints. In 2022–23, for example, battery-grade lithium carbonate prices briefly spiked at six times higher than usual.
Researchers have toyed with replacing lithium with plenty of other charge carriers, including magnesium, calcium, aluminium and zinc, but work on sodium is the most advanced. Sodium lies directly beneath lithium in the periodic table, making its atoms heavier and bigger, but with similar chemical properties. This means a lot of the lessons from lithium battery development and manufacturing can be copied over to sodium. And sodium is much easier to source: it’s about 1,000 times more plentiful in Earth’s crust than is lithium. “Sodium is just unbelievably abundant,” says Ceder, who thinks sodium batteries could end up costing around $50 per kilowatt hour.
Sodium batteries are already in production (see go.nature.com/3tnwdgt). Chinese conglomerate BYD — which in early 2024 replaced Tesla as the world’s largest EV manufacturer — has broken ground on its first sodium-ion battery plant. And Chinese car makers Chery, JMEV and JAC have all announced budget cars powered by sodium-ion batteries in their line-up for China this year. List prices for these small cars are expected to be around $10,000.
On the plus side, sodium’s larger atomic size opens up more options for the metals that can be used in the layered metal oxides at the cathode, says Ceder: “There’s a lot more chemical flexibility.” And researchers could make an anode-less solid-state battery with sodium, too — an enticing possibility, says Nazar.
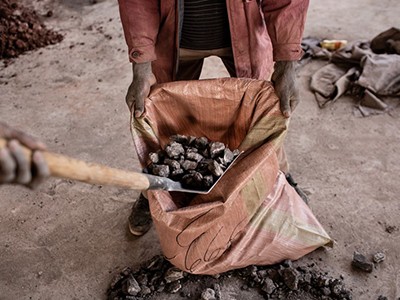
Lithium-ion batteries need to be greener and more ethical
But the heavier weight of sodium compared to lithium makes it fundamentally harder to get to high energy densities. There also hasn’t been as much time to develop the best electrodes and electrolytes — sodium-ion battery energy density now roughly matches that of the best lithium-ion batteries from a decade ago. CATL has a sodium battery that hit an advertised energy density of 160 Wh kg–1 in 2021 at a reported price of $77 per kilowatt hour; the company says that will ramp up to 200 Wh kg–1 in its next model. These lower energy densities mean that range is limited.The ultra-compact cars expected to run on sodium batteries have advertised ranges of around 250–300 km, compared with nearly 600 km for a lithium-powered Tesla Model S.
“It’s going to need chemistry advances in order to get to the level that is necessary for the automotive market in the United States,” says Cunningham, where consumers are used to longer drives and bigger cars.
Some companies, including UK-based Faradion and Swedish Northvolt, are promoting their sodium batteries (also both advertised at 160 Wh kg–1) to store excess renewable energy for electricity grids, where sodium’s weight problem is less of an issue.
Guess and test
Battery development is onerous, because the behaviours of materials are not always predictable. Rupp says, for instance, that it currently takes researchers 8–15 years to come up with new solid-state electrolyte designs and optimize the specifications, including which additives to use and how to pack in high densities of lithium. “This gives me as a material scientist two-and-a-half more materials to work on” before retirement, says Rupp. “That’s too slow”.
Assistance is coming from artificial intelligence (AI) and automated synthesis, which can help to explore more options more quickly. For example, the DoE’s Pacific Northwest National Laboratory in Richland, Washington, is working with Microsoft to rapidly come up with new battery materials; a lithium–sodium solid electrolyte found this way is now in initial tests.
But these AI strategies are limited by the information that chemists have to feed into them, says Nazar. There are still plenty of unknowns, she says, about what’s actually going on at the atomic level at the interface of electrode and electrolyte materials.
In the end, experts say we’re likely to see a range of batteries for our future cars — in much the same way that we have 2-, 4- and 6-cylinder engines today. We might see sodium batteries or LFP for lower-range cars, forklifts or specialist vehicles, for example. Then there might be improved lithium-ion batteries, maybe using silicon anodes or rocksalt cathodes, for mid-range vehicles, or perhaps solid-state lithium batteries will take over that class. Then there might be LiS or even lithium–air cells for high-end cars — or flying taxis. But there’s a lot of work yet to be done. “All of the different chemistries that aren’t commercialized today have their pros and cons,” says Cunningham. “Our job is to remove all those cons.”
"electric" - Google News
February 07, 2024 at 05:13PM
https://ift.tt/2nHaTKc
The new car batteries that could power the electric vehicle revolution - Nature.com
"electric" - Google News
https://ift.tt/Z46t8SR
https://ift.tt/mUVuPbZ
No comments:
Post a Comment